QuickBooks is a popular accounting software that can be used by manufacturing businesses to manage their financial transactions, inventory, and other manufacturing-specific processes. Here is a detailed guide on how to use QuickBooks for manufacturing:
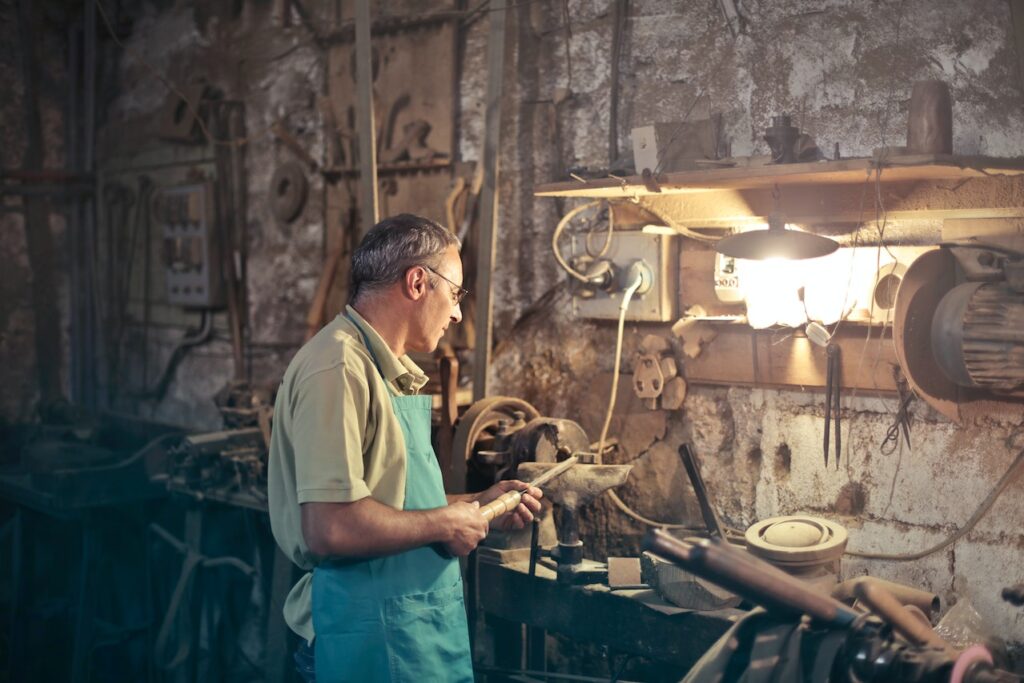
I. Introduction to QuickBooks for Manufacturing
A. Overview of QuickBooks software:
QuickBooks is a popular accounting software developed by Intuit. It provides robust financial management tools for businesses, including manufacturing companies. QuickBooks offers both desktop and online versions, allowing users to choose the option that suits their needs best.
B. Benefits of using QuickBooks for manufacturing businesses:
- Streamlined financial management: QuickBooks simplifies day-to-day financial tasks such as invoicing, expense tracking, and bank reconciliation. It automates processes, saving time and reducing manual errors.
- Inventory management: QuickBooks has built-in inventory tracking capabilities that are crucial for manufacturing businesses. It enables you to monitor stock levels, track costs, and streamline inventory management.
- Cost control and analysis: With QuickBooks, you can track manufacturing costs, including raw materials, labor, and overhead expenses. This allows you to analyze and control costs, aiding in better decision-making.
- Accurate financial reporting: QuickBooks generates various reports, such as profit and loss statements, balance sheets, and cash flow statements. These reports provide insights into your manufacturing business’s financial health and performance.
- Integration capabilities: QuickBooks integrates with a wide range of third-party applications, including inventory management systems, CRM software, and e-commerce platforms. This enables seamless data exchange and process integration.
C. Understanding the features and functionality relevant to manufacturing:
- Inventory tracking: QuickBooks allows you to track inventory levels, record purchase orders, receive inventory, and adjust quantities. You can associate inventory items with specific part numbers, SKUs, and product descriptions.
- Bills of Materials (BOM): QuickBooks supports the creation of BOMs, which define the components and quantities required to manufacture finished goods. BOMs help track raw material usage, costs, and inventory depletion.
- Work orders: QuickBooks facilitates the generation of work orders, providing a structured way to manage the manufacturing process. You can link work orders to specific BOMs and track their progress.
- Cost tracking and job costing: QuickBooks allows you to assign costs to specific jobs or work orders, including direct labor, materials, and overhead expenses. This helps calculate accurate job costs and profitability.
- Sales and invoicing: QuickBooks enables you to create sales orders and invoices for customer orders. You can associate inventory items with sales transactions, track sales revenue, and manage accounts receivable.
- Reporting and analysis: QuickBooks provides a range of pre-built reports for manufacturing businesses. These reports include inventory valuation, cost of goods sold (COGS), profitability analysis, and job costing reports.
- Integration with third-party apps: QuickBooks integrates with various applications that complement manufacturing operations. This includes inventory management systems, CRM software, and project management tools.
Understanding these features and functionalities will help manufacturing businesses leverage QuickBooks effectively, streamline their financial processes, and gain better control over inventory and costs.
Read Also : How To Edit Inventory In QuickBooks Desktop & Online?
II. Setting Up QuickBooks for Manufacturing
A. Selecting the appropriate version of QuickBooks (Desktop or Online):
When setting up QuickBooks for manufacturing, you have two options: QuickBooks Desktop and QuickBooks Online. Consider the following factors to determine the most suitable version for your business:
- Accessibility: QuickBooks Desktop requires installation on a computer, while QuickBooks Online is cloud-based and can be accessed from anywhere with an internet connection.
- Features: Both versions offer core accounting functionality, but there may be differences in certain features. Evaluate the features relevant to your manufacturing business, such as inventory tracking, job costing, and integration capabilities.
- Scalability: Consider the scalability of your business. QuickBooks Desktop is typically more suitable for larger manufacturing businesses with complex needs, while QuickBooks Online is ideal for smaller to mid-sized businesses.
B. Installing and configuring QuickBooks software:
- QuickBooks Desktop:
- Purchase the appropriate version of QuickBooks Desktop (Pro, Premier, or Enterprise) for manufacturing.
- Install the software following the installation wizard instructions.
- Activate your license using the provided product key.
- Set up preferences and customize settings according to your manufacturing business requirements.
- QuickBooks Online:
- Sign up for a QuickBooks Online subscription that fits your manufacturing business needs.
- Create a new company file and provide the necessary business information.
- Set up preferences and customize settings based on your manufacturing requirements.
C. Creating a company file and customizing settings:
- QuickBooks Desktop:
- Open QuickBooks and select “Create a new company” or “Start setup.”
- Enter your company information, such as name, address, and contact details.
- Customize settings, including fiscal year, accounting method, and sales tax preferences.
- Set up bank accounts, credit cards, and other financial accounts relevant to your manufacturing business.
- QuickBooks Online:
- Sign in to your QuickBooks Online account and select “Create a new company.”
- Provide your company details, such as name, address, and industry type.
- Customize settings, such as fiscal year, accounting method, and sales tax preferences.
- Connect your bank accounts and other financial accounts to QuickBooks Online for seamless transaction import.
D. Setting up users and roles for secure access:
- QuickBooks Desktop:
- Go to the “Company” menu and select “Set Up Users and Passwords” > “Set Up Users.”
- Create user accounts for employees who will access QuickBooks and assign appropriate roles (e.g., admin, sales, inventory manager).
- Set user permissions and restrictions to control access to sensitive information and specific features. d. Assign unique usernames and passwords to ensure secure access.
- QuickBooks Online:
- From the QuickBooks Online dashboard, click the “Gear” icon and select “Manage Users.”
- Add users by clicking the “Add user” button and provide the necessary information.
- Assign user roles (e.g., company administrator, standard user, reports-only) to control access levels.
- Set user permissions to restrict access to specific areas and features of QuickBooks Online.
Setting up QuickBooks properly ensures that you have the appropriate version, customized settings, and secure access for your manufacturing business. This foundation allows for effective utilization of QuickBooks’ manufacturing-specific features and streamlines your financial management processes.
Read Also : How To Delete Inventory In QuickBooks Online?
III. Chart of Accounts and Items
A. Reviewing the default chart of accounts:
When setting up QuickBooks for manufacturing, it’s important to review the default chart of accounts provided by QuickBooks. The default accounts may not fully align with your manufacturing business’s needs, so understanding the accounts and their purposes will help you make informed decisions during the customization process.
B. Customizing the chart of accounts for manufacturing:
- Add accounts: Evaluate your manufacturing business’s specific financial needs and add accounts to the chart of accounts accordingly. Common accounts for manufacturing businesses include raw material inventory, work in progress, finished goods inventory, cost of goods sold, direct labor, manufacturing overhead, and sales revenue.
- Modify account names: Adjust account names to accurately represent your manufacturing processes and terminology. For example, rename generic accounts like “Other Income” to “Sales Revenue – Product A” or “Manufacturing Overhead” to “Indirect Labor and Factory Supplies.”
- Subaccounts: Utilize subaccounts to create a hierarchical structure that reflects the relationships between different accounts. For example, you can create subaccounts under “Raw Material Inventory” for specific types of materials.
- Account numbering: Assign account numbers based on a logical structure that makes it easy to navigate the chart of accounts. This can be done by using a numbering system that follows a consistent pattern.
C. Creating inventory items for raw materials, components, and finished goods:
- Open the “Lists” menu and select “Item List.”
- Click “Item” and choose “New” to create a new inventory item.
- Select the appropriate type of item, such as “Inventory Part” for raw materials, components, and finished goods.
- Provide the item details, including the item name, SKU/Part Number, description, unit of measure, cost, and sales price.
- Specify the income and expense accounts associated with the item, such as the sales revenue account and the cost of goods sold account.
- If applicable, set up the preferred vendor for purchasing the item and the reorder point to manage inventory levels effectively.
D. Setting up asset, liability, income, and expense accounts:
- Asset accounts: Customize asset accounts to track relevant assets in your manufacturing business. This may include accounts for cash, accounts receivable, inventory, and fixed assets.
- Liability accounts: Create liability accounts to track obligations and debts. This can include accounts for accounts payable, loans, and credit cards.
- Income accounts: Establish income accounts to track revenue generated by your manufacturing business. You can create separate accounts for different product lines or revenue streams.
- Expense accounts: Set up expense accounts to track various costs incurred in manufacturing operations. This includes accounts for direct materials, direct labor, manufacturing overhead, utilities, and other expenses specific to your business.
Customizing the chart of accounts and setting up inventory items allows you to accurately track and categorize financial transactions in QuickBooks. This level of customization ensures that your manufacturing business’s financial reports provide meaningful insights into your operations and help with decision-making.
Read Also : How To Delete Inventory In QuickBooks Desktop?
IV. Inventory Setup
A. Activating inventory tracking in QuickBooks:
- QuickBooks Desktop:
- Go to the “Edit” menu and select “Preferences.”
- Choose “Items & Inventory” or “Inventory & Assembly” from the left menu.
- Check the box that says “Inventory and purchase orders are active.”
- Click “OK” to save the changes.
- QuickBooks Online:
- From the QuickBooks Online dashboard, click the “Gear” icon and select “Account and Settings.”
- Choose “Sales” or “Advanced” from the left menu.
- In the “Products and services” section, turn on the option for “Track quantity and price/rate.”
- Click “Save” to apply the changes.
B. Defining inventory preferences and settings:
- QuickBooks Desktop:
- Go to the “Edit” menu and select “Preferences.”
- Choose “Items & Inventory” or “Inventory & Assembly” from the left menu.
- Review and modify preferences such as “Inventory and purchase order defaults,” “Advanced Inventory,” and “Costing.”
- Adjust settings according to your manufacturing business’s requirements and click “OK” to save the changes.
- QuickBooks Online:
- From the QuickBooks Online dashboard, click the “Gear” icon and select “Account and Settings.”
- Choose “Sales” or “Advanced” from the left menu.
- Customize settings related to inventory, such as “Quantity on Hand,” “Quantity on Sales Order,” and “Quantity on Purchase Order.”
- Make necessary changes and click “Save” to apply the settings.
C. Entering opening quantities for inventory items:
- QuickBooks Desktop:
- Go to the “Lists” menu and select “Item List.”
- Locate the inventory item for which you want to enter the opening quantity.
- Double-click on the item to open the item details.
- In the “Opening Balance” field, enter the quantity on hand for the item.
- Save the changes.
- QuickBooks Online:
- From the QuickBooks Online dashboard, click the “+” icon and select “Inventory Quantity Adjustment” under the “Other” category.
- Choose the inventory item you want to adjust and enter the opening quantity in the “Quantity Difference” field.
- Save the adjustment to update the quantity on hand for the item.
D. Adjusting inventory levels and valuations:
- QuickBooks Desktop:
- Go to the “Vendors” menu and select “Inventory Activities.”
- Choose the appropriate activity, such as “Adjust Quantity/Value on Hand” or “Build Assemblies.”
- Enter the necessary details, such as the item, quantity, and reason for the adjustment.
- Save the adjustment to update the inventory levels and valuations.
- QuickBooks Online:
- From the QuickBooks Online dashboard, click the “+” icon and select “Inventory Quantity Adjustment” under the “Other” category.
- Choose the inventory item you want to adjust and enter the quantity difference and value difference, if applicable.
- Provide a reason for the adjustment, and add any necessary notes.
- Save the adjustment to update the inventory levels and valuations.
Regularly adjusting inventory levels and valuations in QuickBooks ensures accurate tracking of inventory quantities and values. It allows you to maintain an up-to-date record of your manufacturing business’s inventory, aiding in inventory management and financial reporting.
Read Also : How To Change Date Format In QuickBooks Desktop ?
V. Bills of Materials (BOM)
A. Understanding the concept of a Bill of Materials:
- A Bill of Materials (BOM) is a comprehensive list of components, raw materials, and subassemblies required to manufacture a finished product.
- BOMs specify the quantities of each item needed, along with any additional instructions or specifications.
- BOMs are crucial for planning and tracking the manufacturing process, estimating costs, and managing inventory.
B. Creating BOMs in QuickBooks:
- QuickBooks Desktop:
- Go to the “Lists” menu and select “Item List.”
- Click the “Item” button and choose “New” to create a new item.
- Select “Inventory Assembly” as the item type.
- Enter the name and other details for the assembly item.
- In the “Bill of Materials” section, add the components and quantities required for the assembly.
- Save the item to create the BOM in QuickBooks Desktop.
- QuickBooks Online:
- From the QuickBooks Online dashboard, click the “+” icon and select “Product/Service” under the “Customers” or “Sales” category.
- Choose “Inventory” or “Non-inventory” as the type, depending on your preference.
- Enter the name and other details for the product or service.
- In the “Bill of Materials” section, add the components and quantities required for the assembly.
- Save the item to create the BOM in QuickBooks Online.
C. Linking BOMs to inventory items:
- QuickBooks Desktop:
- Open the inventory assembly item created for the BOM.
- In the “Bill of Materials” section, select the appropriate inventory items from the dropdown menu or search for them.
- Enter the quantities required for each component in the assembly.
- Save the changes to link the BOM to the inventory items.
- QuickBooks Online:
- Open the product or service item created for the BOM.
- In the “Bill of Materials” section, select the appropriate inventory items from the dropdown menu or search for them.
- Enter the quantities required for each component in the assembly.
- Save the changes to link the BOM to the inventory items.
D. Managing revisions and updates to BOMs:
- QuickBooks Desktop:
- When a revision or update is necessary, open the inventory assembly item linked to the BOM.
- Make the necessary changes to the components or quantities in the “Bill of Materials” section.
- Save the changes, and QuickBooks will prompt you to create a new revision or update the existing one.
- QuickBooks Online:
- To manage revisions or updates to a BOM in QuickBooks Online, you can create a new product or service item with the updated BOM.
- Make the necessary changes to the components or quantities in the new BOM.
- Update any related inventory items or product listings to reflect the changes.
Managing revisions and updates to BOMs is crucial to ensure accuracy in manufacturing processes. By creating and linking BOMs in QuickBooks, you can track the required components, streamline production, estimate costs, and maintain accurate inventory records.